What does pharmaceutical manufacturing have to do with race car driving? For Sanofi, the connection is agility. In 2022, Sanofi partnered with McLaren Racing to adapt Formula 1 pit stop methods, advanced analytics, and simulation to speed manufacturing equipment changeover. It also partnered with Veeva to implement quality solutions to modernize and connect operations and partners across the value chain.
Fundamental to Sanofi’s strategy are digitized manufacturing and supply networks that connect the company’s quality team with CDMOs, suppliers, and contract partners, and strong links from process development and technology transfer to manufacturing. “We’ve had to simplify, standardize, and digitize to enable data-driven decisions,” says Maité Durrenbach, chief quality officer.
With these innovations, Sanofi is enabling a more nimble response to external change, so that it can deliver innovative treatments to patients faster. In 2022, the company launched QualiPSO, a quality transformation program to ensure agile quality management and a focus on data integrity and value-added efforts. Veeva QMS and Veeva QualityDocs are the core of the QualiPSO system.
The project’s scope was challenging, involving over 40 manufacturing sites,12,000 CMOs, more than 100 legacy quality applications, and global documentation in more than 14 languages. However, results so far have defied skeptics. “We have made fundamental changes quickly and with minimal risk,” says Helene Nogent-Coste, head of Sanofi’s QMS program.
Benchmarking to set new quality goals
Initially, Sanofi’s quality team leaders worked with a consulting firm and a network of industry peers to benchmark its quality management systems. Efforts focused on the 17 most important areas, and resulted in the following goals:
- Prioritize quick closure of the most significant quality deviations
- Reduce the number of steps and people required to manage change control
- Measure CAPA efficiency and the connection between change control and document management.
- Eliminate redundancies between global and local SOPs by reducing local “clone” documents
- Designate a primary site to manage activities with specific suppliers (e.g., for quality agreements) to avoid duplication of efforts by multiple sites
- Standardize QC, leveraging digital core models, boosting instrument connectivity, and automating processes.
Meeting these targets promised to bring greater efficiency and productivity, more consistent processes, and improved QC and compliance. However, a complex landscape of legacy systems and disconnected solutions made it challenging to achieve, explains Nogent-Coste. In addition, the core models that supported quality management were outdated and expensive, says Philippe Barrau, leader of Sanofi’s digital QMS program and product line.
Standardizing and aligning processes
Sanofi’s quality leaders decided to standardize business processes on Veeva’s Vault Quality – Veeva QMS and Veeva QualityDocs – to improve end-to-end processes and ensure their alignment with core models and values. Quality leaders ensured that the team focused on agility, and took a minimum viable product approach to implementation that prioritized essential efforts yet allowed other, incremental improvements to be made. A self-directed network of business process owners set targets and defined simpler and more efficient ways of working within each of their areas, increasing end-user involvement, and, ultimately, adoption.
As shown in Figure 1, QualiPSO is integrated in the SANOFI systems landscape, as data provider and consumer. It includes the Veeva Quality-to-RIM connector to improve collaboration between quality and regulatory teams, as well as 30 internal systems, including:
- ERPs to enable batch release
- An external training system
- An application called TransPerfect for live translation, which allows users to work on translation documents directly within Veeva Quality.
All data is stored in a data lake, allowing users to report on trends, follow up on production and product quality, and manage batch releases.
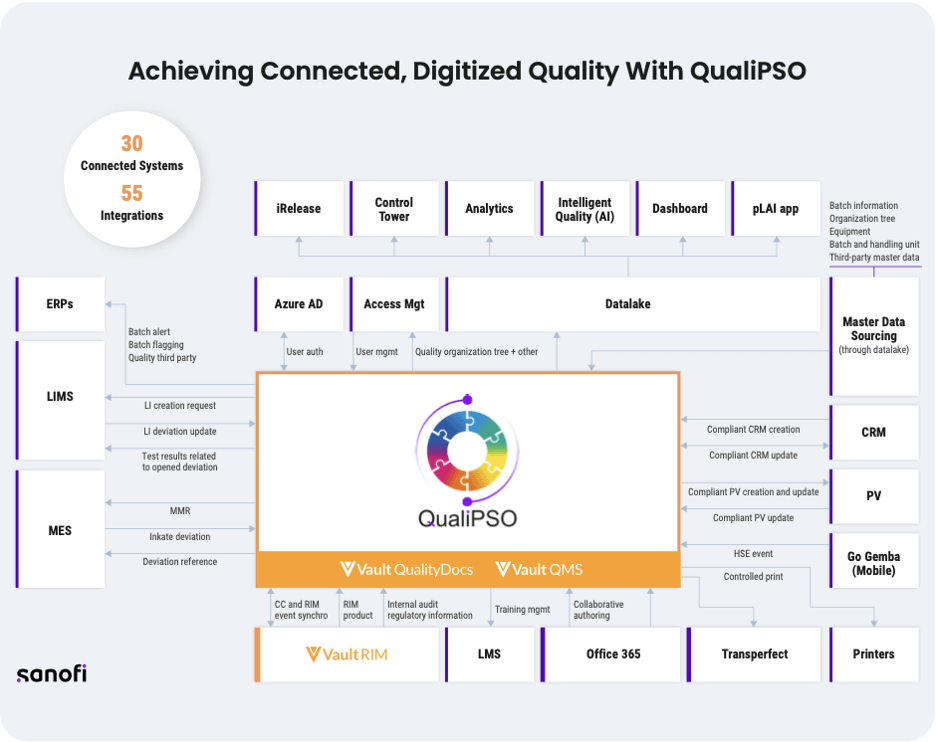
New KPIs and increased efficiency
The new system is being used across 200 entities by 83,000 quality documentation and 30,000 QMS users. Sanofi’s quality team has developed KPIs that reflect the project’s original goals, including:
- Cycle-time reductions for deviations in audits
- Speed of the fast-track complaint-adoption process
- Total release time
- Release time per batch
- Reduction of local procedures
The new quality ecosystem has improved efficiency by eliminating non-value-added work. It also prevents data duplication to ensure data integrity, and enables end-to-end, connected quality processes.
Key results achieved include:
- Increased adoption, with 83,000 quality documentation and 30,000 QMS users in 200 locations
- Consolidated forty legacy systems into one unified system, which now manages 14 quality processes
- Reduced change-control steps from 11 to 5; reduced local documents from 7,000 to 50
- Enabled 60% of deviations to be closed on a “fast-track” basis.
- Reduced document display time from 20 seconds to 1 second
Sanofi is working closely with Veeva on new features including a new system for managing third-party complaints and an application that would automate the creation of impact-assessment records. The quality team is also using an external tool that leverages AI to manage complaints and an automated system for third-party complaints.
In the future, they plan to use automation to detect the sites affected by complaints and advanced algorithms to categorize and prioritize tasks and emails. An automated program that integrates with databases and systems to identify audit targets and help assign resources more effectively is also in development.
Innovative approaches encourage user adoption
Change management has been an important focus at every stage of the QualiPSO effort, with process training managed by communities of practice within individual business groups. Post-deployment coaching efforts have been important in ensuring that users are comfortable with the new tools and approaches and that they use them correctly and consistently.
Three months before “go live,” Sanofi enabled experiential learning by giving users access to the system in a sandbox environment so they could experiment with it without risk.
These efforts have paid off. Nogent-Coste says users are pleased with the new system, particularly its speed. Displaying a document once required 20 seconds, but now takes less than a second. And in drug manufacturing–as in racing–every one of those seconds counts.
Learn more about Veeva Quality Cloud
More Customer Stories
Watch Video
Watch Video
Watch Video