How UCB and Other Biopharmas Made the Case for Safety Transformation
Although many safety and pharmacovigilance (PV) professionals struggle with the shortcomings of legacy safety solutions, the path toward better systems can be unclear. Transforming an organization’s safety technology landscape can be a lengthy and labor-intensive process, including:
- Identifying a system that meets company needs
- Making a business case to move to a new system
- Defining a new safety strategy
- Managing a migration and go-live
While safety transformation may seem daunting, companies of various sizes have embarked on these journeys successfully to drive operational efficiencies, lay the foundation for innovation and safety intelligence, or better meet regulatory demand. UCB, and two biopharmas – three companies at different points in their safety journeys – shared how they made a case for safety transformation within their organizations. As a dermatology biopharma’s vice president of R&D process optimization said, “It’s challenging to change systems, but it also allows you to rethink your safety processes and see where you can optimize. We were seen as a reactive unit: we see a signal, then react. We wanted to become a safety intelligence unit.”
Companies can reap the benefits of modernizing their safety systems quickly. In less than a year, one global biopharma saw a 40% reduction in its number of procedures and easier compliance with current and future regulatory requirements.
Moving to a unified, cloud-based approach for safety
The five drivers for safety transformation
Meet regulatory demand | Foundation for innovation | Better decision-making | Operational efficiencies | Enable cross-functional processes |
---|---|---|---|---|
Making it easier to meet increasing, new, and changing regulations | Centralizing processes and standardizing data to create a foundation for AI and deeper analytics | Eliminating reconciliation and supporting better decisions | Increasing operational efficiencies with automation and reduced overhead | Enable and simplify cross-functional processes with end-to-end automation |
The ability to leverage connections between Veeva Vault applications across clinical, regulatory, quality, and medical led UCB to look into Veeva Safety, says the company’s Head of Digital Technology Patient Safety Jonas Maselis. In UCB’s case, the company had “the time and space to do things right,” he explains. “We’re taking a staged approach and clearly defined objectives.”
In contrast, the dermatology biopharma had a hard deadline to go-live. “Veeva Safety was an obvious choice because we essentially had the entire Veeva platform already and wanted to leverage the connections,” says the company’svice president of R&D process optimization .
The head of systems and innovation at a global biopharma felt similarly when looking at safety systems. In 2023, the company shifted its strategy to consolidate its technology landscape and simplify processes. “We wanted to work smarter, not harder. To get there, we needed to simplify and innovate,” she says. “This helped us optimize our resources and make data-driven decisions that drive strategic value.”
This need led the company to Veeva Safety. “We wanted to make the most out of our system,” she explains. “We wanted to have these connections, not just within pharmacovigilance, but across the organization wherever possible.”
Becoming a strategic partner across R&D
Although UCB and the two biopharmas have varied strategies, all three have a strong vision for safety that they defined early on in their transformation journeys. For the UCB team, their safety vision needed to fit into the company’s larger R&D vision. This meant partnering with Veeva to maintain compliance while improving automation, processes, signal detection, and insight generation. As an early adopter of Veeva Safety Signal and Safety Workbench, UCB is looking to “improve data quality and transparency around signal tracking,” says the company’s Head of Systems Adrian Maynier. “We also want to make our data more accessible and improve our analytics.” This includes standardizing their terminology, increasing data quality, and improving communications to health authorities.
The dermatology biopharma is also exploring a unified R&D strategy beyond safety. Its vice president of R&D process optimization is focused on moving safety beyond compliance, encouraging her team to partner with clinical and commercial teams. “Compliance is something we have to do, but PV has more value to offer the organization,” she says. Potential opportunities where safety could contribute include proactively sharing insights on side effects; learning from adverse events, real-world, and genomic data to support researchers as they address risks during protocol design; collaborating with medical affairs on key opinion leader outreach; and boosting support during the authorization and post-marketing phases.
Modern safety technology is helping the company push toward that strategic vision. “Before, our only focus was mailing cases and putting reports together in time to ship to authorities,” the vice president of R&D process optimization remembers. “Now, technology is advancing and we have more opportunities to think strategically.” For example, during post-marketing, the safety team may identify that certain patient groups report fewer side effects than other cohorts. These insights could enable commercial teams to focus their efforts on patient groups that would benefit most from the product. They may even help secure a better price when negotiating with payers.
For the global biopharma, simplifying its PV systems landscape is the main priority. The company started its journey by going live with core safety processes, focusing on compliance and standardizing processes. As its transformation journey continues, the company will implement additional configurations and leverage upgrades in Veeva Safety’s three releases per year. “Within the next two years, we hope to have all of our safety processes harmonized in Veeva Safety. This will create the foundation for innovation,” says the company’s head of systems and innovation.
Leveraging safety data to drive strategic decisions
The UCB team is looking forward to long-term, incremental improvements from the safety systems they’ve set in place. Maselis is especially excited to switch from on-premise IT infrastructure to a cloud-based platform that includes Veeva Safety as well as clinical, quality, regulatory, and medical applications. “From an IT perspective, I’m looking forward to leveraging data from other Vaults. I’d like to understand how that data flows and what value it brings when it’s brought together,” he says. Maselis also hopes to use automation to get to low-touch case processing.
The global biopharma is farther along in its safety transformation journey. In just ten and a half months, the company migrated 12.5 million documents and 3.1 million cases across three legacy systems into Veeva Safety. “We became stronger because we transformed our PV processes. We now have one global solution for local safety officers and global teams. Everyone works in the same system. And, all our processes are aligned across global and local PV teams,” says the company’s head of systems and innovations.
Having a centralized system where PV professionals can easily track their progress has improved the dermatology biopharma’s global collaboration. “Now, everyone knows what’s coming, and what needs to be done. If a case is taking longer than they would expect, we can see it and work on it as a team,” says the vice president of R&D process optimization.
Since going live in June 2023, the dermatology biopharma has seen a positive response from its affiliates. “Our affiliates are our happiest users because Veeva Safety makes their lives much easier. It creates transparency while eliminating local logs and reconciliation,” says the vice president of R&D process optimization.
Now that affiliates work in one system, the dermatology biopharma has streamlined local and global case processing. Affiliates can reuse local case content for global cases, eliminating the time spent duplicating and reconciling content. They also have greater visibility into when cases will arrive. “Before, countries were just waiting without knowing when, or if, a case would arrive. Now, they can act on it right away when cases are approaching their deadline,” says the vice president of R&D process optimization. “With Veeva Safety, we have real-time visibility into adverse events and data transparency that helps us work even better together.”
Evolving beyond compliance to data-oriented safety
In recent years, Maynier has found that inspections are becoming increasingly data-oriented. He believes having a safety system that can quickly and efficiently provide reports and analytics will help UCB improve its inspection readiness. Maselis echoes Maynier’s sentiments. He is particularly interested in improving the traceability of UCB’s data beyond safety, such as regulatory actions in Veeva RIM. “Just like you can track an Amazon package until it reaches your house, I want to see the downstream activities like submissions of an updated risk management plan or clinical protocol stemming from safety insights. Having that visibility and traceability is important,” says Maselis.
The dermatology biopharma is also focused on improving traceability. “In a recent inspection in France, they said ‘Okay, you received this case on this date. Where did it go? Where did it end up? Is it a signal? Do you have it in the PSUR?’ They followed the case from beginning to end,” explains the vice president of R&D process optimization.
Having a unified platform made it much easier for the inspector to find that information because they no longer need reconciliation or logs. “The inspector was pleasantly surprised,” says the vice president of R&D process optimization. “Initially, she asked ‘Where is the log?’ but we showed her that there is no need for a log because we already have all the information in one place.”
Leveraging safety to improve business outcomes
No department can do its job alone. Clinical feeds data, like study information and serious adverse events, to safety teams. Safety provides data and documents, like aggregate reports to regulatory teams for submission to health authorities.
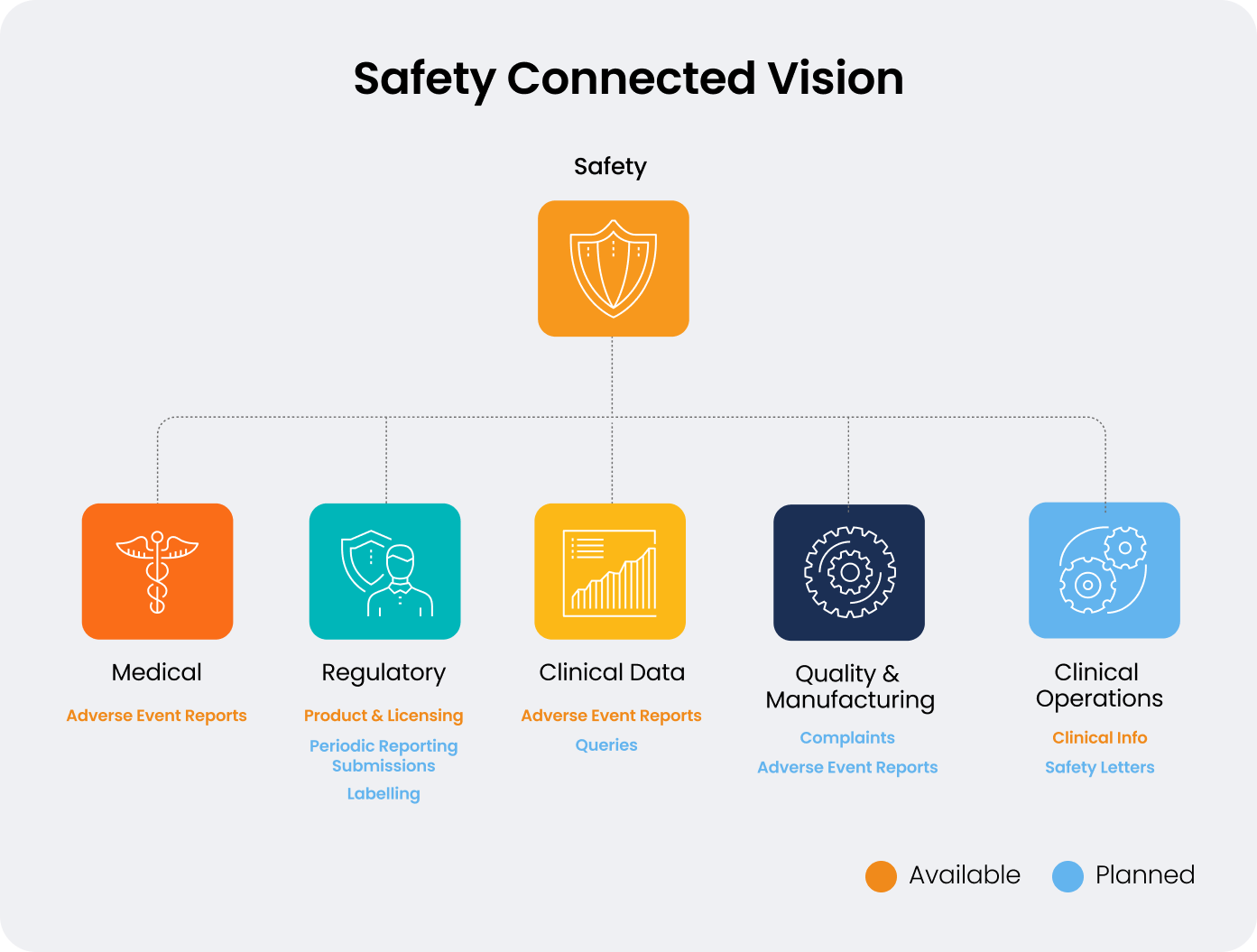
Now that the two biopharmas have successfully modernized their safety systems, the companies are looking beyond drug safety to improve outcomes across the business.
Veeva Safety freed up time for the dermatology biopharma to operate as strategic partners, enabling collaboration on activities like risk management, and product labeling. “Veeva Safety helped us open up dialogues with other departments,” says the vice president of R&D process optimization. For example, the PV team can assess the listedness of cases directly from Veeva RIM. This ensures that they always have the latest version. They’re also working with their regulatory teams to harmonize their Vault processes for managing local labels.
The PV team at the global biopharma is working on similar initiatives. “Now that we are live, we want to see how we can take full advantage of what Veeva has to offer,” says its head of systems and innovations. “We want to take the static data we have today in different systems and connect it to drive even greater value.” This includes automating previously manual processes, like case intake and triage, data entry, quality control, and medical review. The company has made significant progress in automating case intake, distribution, and submission, with an ultimate goal of reducing time spent on individual case study reports by 20% year over year.
The connected systems landscape these companies put in place will help lay the foundation for further innovation. “We want to get to one source of truth,” says the head of systems and innovations at a global biopharma. “We’re looking forward to reducing the need for reconciliation, maintenance, and duplicity that we have today.” Maynier from UCB team shares a similar sentiment: “We’ll sit here and look back in five years and say, ‘Do you remember how we used to work back in 2024? How archaic were we?’”
Hear more about UCB’s vision for safety transformation through simplified and automated PV processes.